在生物醫(yī)學(xué)、食品工業(yè)、材料科學(xué)等領(lǐng)域,定制液氮桶憑借其 - 196℃的超低溫環(huán)境與靈活的設(shè)計,成為樣本儲存、冷凍加工及材料處理的核心設(shè)備。然而,實際使用中因定制需求的復(fù)雜性,常出現(xiàn)保溫性能不足、密封性失效、操作風(fēng)險高等問題。本文結(jié)合行業(yè)實踐與技術(shù)標準,深入剖析這些問題的根源,并提出針對性解決方案。
定制液氮桶的核心保溫機制是高真空多層絕熱(HVMI),通過抽離夾層空氣并設(shè)置鋁箔反射屏,將熱傳導(dǎo)率降低至 0.001 W/(m?K) 以下。但實際使用中,真空度會隨時間自然下降,導(dǎo)致日蒸發(fā)率從初始的 0.2%-0.5% 逐漸升高。例如,某實驗室定制的 30L 液氮桶在使用 18 個月后,因真空度降至 10?2 Pa,日蒸發(fā)量從 0.8L 增至 2.1L,顯著增加補液頻率與成本。
解決方案:
- 定期真空檢測:每半年通過氦質(zhì)譜檢漏儀檢測真空度,確保其≤2×10?2 Pa。
- 真空自修復(fù)技術(shù):選擇采用真空度自修復(fù)涂層的液氮桶,如海爾生物醫(yī)療的智芯系列,通過納米材料自動填補微小漏點,延長真空壽命至 10 年以上。
杭州余杭等濕熱地區(qū),夏季高溫高濕環(huán)境(如 30℃、濕度 70%)會導(dǎo)致液氮桶外壁結(jié)霜,形成 “熱橋效應(yīng)”。以 175L 液氮桶為例,在持續(xù)高濕環(huán)境中,外部冷凝水每日可增加 0.5L 的額外熱負荷,使液氮揮發(fā)率提升 15%-20%。
應(yīng)對策略:
- 防潮設(shè)計升級:在真空夾層外增加氣凝膠防潮層,其憎水率>99%,可有效阻止冷凝水滲透。
- 動態(tài)溫控補償:集成環(huán)境傳感器,當濕度>60% 時自動啟動內(nèi)置加熱絲,維持外壁溫度在露點以上,避免結(jié)霜。
液氮桶的頸塞、閥門及管道連接處通常使用氟橡膠(Viton)或硅膠密封圈。氟橡膠耐溫范圍為 - 20℃至 200℃,但在 - 196℃液氮環(huán)境中,其彈性模量會增加 3 倍,導(dǎo)致密封失效。某食品企業(yè)定制的自增壓液氮桶,因密封圈材質(zhì)選擇不當,在速凍過程中頻繁出現(xiàn)微泄漏,造成液氮損失率高達 3%/ 小時。
優(yōu)化方案:
- 耐低溫材料替換:采用聚四氟乙烯(PTFE)與硅膠復(fù)合密封圈,可在 - 200℃保持彈性,泄漏率<1×10?? Pa?m3/s。
- 密封結(jié)構(gòu)改進:采用雙 O 型圈 + 彈簧補償設(shè)計,通過機械彈性抵消材料低溫收縮,確保動態(tài)密封穩(wěn)定性。
工業(yè)場景中,液氮桶常需與深冷箱、速凍機等設(shè)備通過金屬軟管連接。若軟管長度過長(如>5m)或彎曲半徑過小(<300mm),會因熱脹冷縮產(chǎn)生機械應(yīng)力,導(dǎo)致螺紋接頭松動。某半導(dǎo)體工廠在晶圓冷卻過程中,因軟管安裝不當,每班次發(fā)生 2-3 次泄漏,被迫停機檢修。
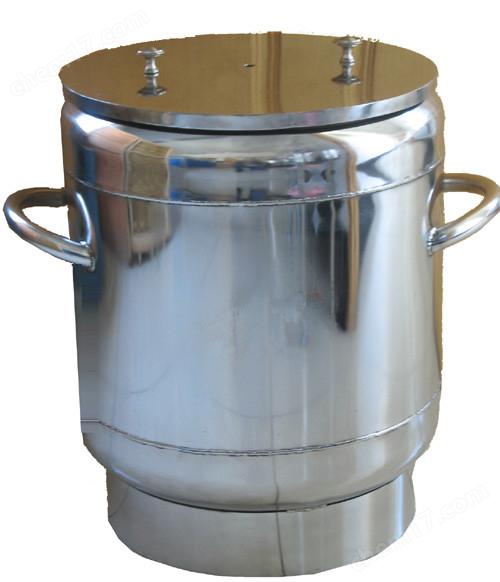
工程實踐:
- 柔性連接優(yōu)化:選擇內(nèi)徑 25mm、彎曲半徑≥5 倍管徑的金屬軟管,并在兩端加裝防震固定支架,減少振動傳導(dǎo)。
- 智能泄漏監(jiān)測:在連接處集成壓力傳感器,當壓力波動超過 ±5% 時,通過 NB-IoT 模塊實時推送報警至運維人員手機。
定制液氮桶的容量選擇需基于日均使用量精確計算。例如,某實驗室每周消耗 15L 液氮,若定制 10L 罐體,需每 3 天補液一次,增加操作風(fēng)險;而選用 30L 罐體則導(dǎo)致 50% 的空間浪費。此外,口徑設(shè)計直接影響操作便利性:80mm 以下口徑難以容納 9×9 規(guī)格凍存盒,而 216mm 大口徑會使日蒸發(fā)率增加 0.8L。
設(shè)計原則:
- 容量公式推導(dǎo):罐體容量 =(單次最大使用量 × 安全系數(shù) 1.5)/ 靜態(tài)保存期 × 動態(tài)使用頻率。
- 口徑分級適配:醫(yī)療樣本存儲建議 50-80mm 口徑,工業(yè)冷裝配則需 125-216mm 大口徑。
自增壓液氮桶在工業(yè)場景中需輸出 0.08-0.15MPa 壓力,但壓力調(diào)節(jié)閥若未按 GB/T 5458-2012 標準校準,可能導(dǎo)致超壓。某汽車零部件廠曾因壓力閥失效,罐體壓力驟升至 0.3MPa,觸發(fā)防爆膜破裂,造成 1.2 萬元直接損失。
安全強化:
- 雙重壓力保護:配置機械式安全閥(開啟壓力 0.12MPa)與電子壓力傳感器(閾值 0.1MPa),實現(xiàn)冗余控制。
- 防爆結(jié)構(gòu)優(yōu)化:采用爆破片與安全閥串聯(lián)設(shè)計,爆破片破裂壓力≤0.15MPa,且破裂后自動觸發(fā)聲光報警。
疫苗運輸用液氮桶需滿足 IATA 航空運輸標準,其抗震性能需通過 8 級顛簸測試(加速度≤1.5g)。某醫(yī)療企業(yè)定制的 10L 運輸罐因未采用內(nèi)膽支撐結(jié)構(gòu),在模擬運輸中液氮飛濺,導(dǎo)致疫苗效價損失 12%。
技術(shù)突破:
- 抗震模塊化設(shè)計:內(nèi)膽通過三點式不銹鋼支架固定,配合底部緩沖橡膠,可承受 3m 跌落沖擊。
- 合規(guī)認證保障:選擇通過 CE、ASME BPVC 等認證的液氮桶,確保運輸過程中溫度波動≤±2℃。
食品速凍用液氮桶若未采用 316 不銹鋼內(nèi)膽,長期接觸鹽水等腐蝕性介質(zhì)會導(dǎo)致內(nèi)壁銹蝕。某海鮮加工廠定制的 500L 液氮罐,因使用 304 不銹鋼,6 個月后內(nèi)膽出現(xiàn)麻點狀腐蝕,被迫提前更換,損失達 5 萬元。
材料革新:
- 超耐腐蝕材料:選用含鉬量 2.5%-3% 的 316L 不銹鋼,其耐鹽霧腐蝕時間>1000 小時,是 304 不銹鋼的 3 倍。
- 內(nèi)壁拋光處理:采用電解拋光工藝(Ra≤0.2μm),減少微生物附著,符合 FDA 食品接觸標準。
通過集成溫濕度傳感器、液位計與壓力變送器,定制液氮桶可實現(xiàn)全參數(shù)實時監(jiān)測。例如,四川賽爾微訊的罐聯(lián)網(wǎng)平臺能同時管理 200 + 液氮桶,當任一罐體液位<20% 時,自動觸發(fā)自增壓補液系統(tǒng),并向管理員推送 3 級報警(短信、APP、郵件)。
基于歷史數(shù)據(jù)的機器學(xué)習(xí)模型,可預(yù)測密封圈老化周期。某生物樣本庫通過分析 3 年數(shù)據(jù),將密封圈更換周期從固定的 12 個月延長至 18 個月,同時將泄漏率從 0.7 次 / 年降至 0.1 次 / 年。
針對工業(yè)場景的高能耗需求,帶有汽化冷量回收功能的液氮桶可將汽化熱用于冷卻其他工藝流體。某半導(dǎo)體工廠采用該技術(shù)后,液氮利用率從 65% 提升至 82%,年節(jié)約能耗成本 12 萬元。
- 技術(shù)參數(shù)清單:明確容積(1L-175L)、口徑(30mm-216mm)、工作壓力(常壓 - 0.3MPa)及靜態(tài)保存期(15-110 天)。
- 場景參數(shù)固化:如運輸場景需明確振動等級(如 ISO 16750-3)、存儲場景需定義環(huán)境溫濕度范圍(如 - 40℃至 + 50℃)。
- 真空度檢測:采用氦質(zhì)譜檢漏儀,確保夾層真空度≤2×10?2 Pa,泄漏率<5×10?? Pa?m3/s。
- 絕熱層驗證:通過紅外熱成像儀檢測罐體表面溫差,確保任意點溫升≤2℃/ 小時。
- 定期維護套餐:包含每年 1 次真空度檢測、每 2 年 1 次密封圈更換、每 5 年 1 次內(nèi)膽探傷等項目。
- 退役處理方案:液氮桶報廢前需進行氮氣置換與真空破壞,確保無殘留液氮與壓力風(fēng)險。
定制液氮桶的高效使用,需從材料選擇、結(jié)構(gòu)設(shè)計到智能化管理進行系統(tǒng)性優(yōu)化。通過遵循 GB/T 5458-2012 等標準,結(jié)合行業(yè)特性與地域環(huán)境(如杭州余杭的濕熱氣候),采用真空自修復(fù)、耐低溫密封、物聯(lián)網(wǎng)監(jiān)控等技術(shù),可顯著提升設(shè)備可靠性。未來,隨著氣凝膠絕熱、AI 預(yù)測性維護等技術(shù)的普及,定制液氮桶將向 “零蒸發(fā)、零風(fēng)險、零干預(yù)” 的終極目標邁進,為生物醫(yī)學(xué)、高端制造等領(lǐng)域提供更可靠的低溫保障。